Making technology and precision processing of new bearing materials with increased wear resistance based on alloy steels wastes
Developed technology and precision processing of composite self lubricant bearing materials for heavy duty exploitation conditions based on alloy steels wastes with solid lubricant allows to manufacture new parts which essentially exceed known bearings over wear resistance for analogue conditions. Created technology is based at use of powder technological operations in combination with fine machining of friction parts. By research results the algorithm of calculating the pressing parameters of bearing bushes have been developed on the base of plasticity theory, the technological parameters of sintering have been worked through and optimized for new sliding bearings blanks. It allows to control of materials’ structure and properties. Establishment of an influence of making technology for formation of antiscoring friction films at high-temperature and high-speed wear allows to realize purposeful tribosynthesis of friction films that determines high wear resistance of part at heavy duty exploitation conditions at friction without lubricant.
Calculated mathematical dependences allowed to obtain the computer simulations of technological parameters of working surfaces fine grinding. They take into account cutting effect of abrasive grains totality for formation of part’s surface relief at super difficult grains’ motion path at working zone of grinding.
Developed technological techniques allow prognosticately to create and control by formation of new composite bearings working contact surfaces’ microrelief for ensuring of high quality parameters of surfaces which are precondition of high wear resistance for new friction parts at heavy duty exploitation conditions.
By research results new model technological processes have been developed and development batch of bearing bushes from regenerated raw materials have been manufactured for application on machinebuilding plants. Summary economic effect from application of research results come to more than 200 thousands hrn. per year.
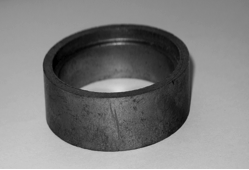
Вложение | Размер |
---|---|
![]() | 1.04 МБ |