Development of the process production partially metallized iron-ore burden materials on the base ore-carbonic composition for traditional metallurgical technology
For the reason increasing of metallurgical value charge materials domain production was researched possibility of the reception partly metallize pallets from ore-flux-fuel composition. As main raw material was used iron-ore concentrate Inguleckogo GOKa (64,7 % Fe), with additive coke breeze of fraction 0-3 mm and quicklime, which then mingled and were granulated on plate granulator. Got pellets (with 12-17 % dispersed carbon) after fixing on surface defensive layer by thickness 2,0-2,5 mm from mixture of the concentrate and quicklime (1:1) mingled with solid fuel. The fuel was characterized by certain functional distribution in layerwise system: an activate fuel 0-3 mm, in clearance between granule – main or works 3-7 mm and more large – 7-10 mm, as fuel of curing.
Baking of pellets with solid propellant packed was conducted in laboratory installation, equipped with by cylindrical chalice 100 and 200 mm at height sintered layer 250-380 mm. Herewith in layerwise system of solid propellant packed was formed as follows: on fire grate of the chalice packs solid propellant substrate, consisting of two layers coke breeze of fractions 0-10 mm. The first layer – a layer activate fuel, which is set fire to by gas burner in mode of the filtering; is it them translated in blast mode and on surface burning layer packs the layer a worker fuel. On actuated surface of solid propellant substrate pack the layers of pellets with simultaneous filling space between granules of solid propellant packed. The masses fuel on layer will change and present the subject to optimization; herewith their amount must be adequately expenses on processes, which occur in layer of the granules, located on them.
Need worker layer of the solid fuel is dictated, as minimum, two circumstances. The first – a creation corresponding to is hawed a temperature-heat mode of baking and metallized of the granules. Second – a creation reconstruction-heat mode. The fuel substrate as a whole executes the role of the external source of the heat with controlled composition of heat-carrying. At achievement of the temperature in layer 1423-1473 K (in zone of the combustion 1595-1613 K) is conducted endurance under minimum amount of the air, given in layerwise system, with the following cooling of sintered material.
The called on experiments on given methods has shown the possibility of the reception during 35-40 min. partly metallize charge of the material at presence in kernel of the granules 12 % carbon and height sintered layers 4-5 d granules, which are situated between workers (generative) layer fuel.
The realization designed technological scheme on conveyor roasting machine at height sintered layer 0,25-0,3 m in mode filtering under of depression 200-400 mm.wat.col. allow to get hybrid agglomerate iron-ore material in the manner of druse with remaining carbon for the following domain redistribution, sufficient «cool» toughness, degree to metallize 30-35 %, output suitable 75-80 % and reduction of the expenses of the natural gas in 1,5-2,0 times.
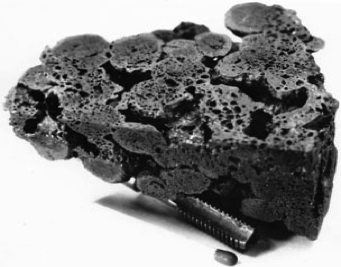
Вложение | Размер |
---|---|
![]() | 117 КБ |