Підвищення продуктивності виготовлення та якості виробів в формоутворюючих процесах холодного листового штампування
Зменшення кількості переходів виготовлення виробів або збільшення ступеню деформації за один перехід в формоутворюючих процесах листового штампування дозволяє підвищити продуктивність виготовлення та робить отриману продукцію конкурентоспроможною.
В процесах витягування розроблені способи формоутворення з прикладанням диференційованого радіального підпору фланця за допомогою рідини, витягування в матриці спеціального профілю та комбінованого витягування в двоконусній матриці спеціального профілю. З використанням комп’ютерного моделювання методом скінчених елементів встановлено, що прикладання підпору суттєво зменшило величину розтягувальних напружень в небезпечному перерізі, які приводять до руйнування стінки. Зменшення вказаних напружень дозволило збільшити ступінь деформації за один перехід і зменшити кількість переходів витягування. Використання традиційного витягування в матриці спеціального профілю та комбінованого витягування в двоконусній матриці спеціального профілю також дозволило скоротити кількість переходів штампування. Проведені експериментальні дослідження підтвердили результати розрахунків. Отримані аналітичні залежності для визначення параметрів комбінованого витягування в двоконусній матриці;
Для процесів обтиску трубчатих і порожнистих заготовок з дном було використане прикладання протитиску за допомогою рідини на внутрішню поверхню заготовок та застосований обтиск в матриці спеціального профілю. Розрахунком встановлено, що прикладання протитиску при обтиску трубчастих заготовок із сталі приводить до виключення втрати стійкості стінки заготовки та утворенню поперечних гофр на стінці та здеформованій частині заготовки, що дозволило отримувати вироби з горловиною за один перехід.
Застосування конусних матриць спеціального профілю, в яких деформуюча поверхня утворена перетином кіл постійного діаметру, центри яких розташовані під кутом з певним кроком, забезпечило зменшення впливу сил тертя при формоутворенні та збільшення ступеню деформації за один перехід. Використання попередньої операції профілювання стінки трубчастих або порожнистих заготовок з дном приводить до отримання обтиском виробів з постійної товщиною стінки. Експериментальні дослідженнями отримані дослідні зразки виробів, що підтвердило дані розрахунків. Отримані аналітичні залежності для визначення зусилля обтиску, форми та розмірів здеформованої частини заготовки
Розроблений спосіб відбортування отворів в листових заготовках та профілях забезпечує отримання здеформованої частини з постійною товщиною стінки без викривлення. Постійна товщина стінки приводить до збільшення висоти виробів після відбортування з потоншенням та підвищення надійності і довговічності роз’ємних та нероз’ємних з’єднань отриманих виробів з іншими деталями. Використання попереднього профілювання листових заготовок та профілів шляхом формоутворення отворів холодним видавлюванням з подальшим пробиванням перемички приводить до економії металу. Розрахунком та експериментом показана можливість отримання стінки постійної товщини. Для інженерних розрахунків параметрів попереднього профілювання заготовок та параметрів відбортування отримані аналітичні залежності для визначення силових режимів, питомих зусиль на деформуючому інструменті та кінцевих форми та розмірів здеформованих заготовок.
Для отримання фланців різноманітної конфігурації на трубчастих заготовках та трубах розроблений спосіб роздачі пуансоном спеціального профілю. У такого пуансону деформуюча поверхня утворена перетином кіл постійного діаметру, центри яких розташовані під кутом з відповідним кроком. Комп’ютерним моделюванням встановлений та підтверджений експериментом профіль пуансону, який забезпечує зменшення впливу сил тертя на формоутворення при роздачі та збільшення коефіцієнта роздачі.
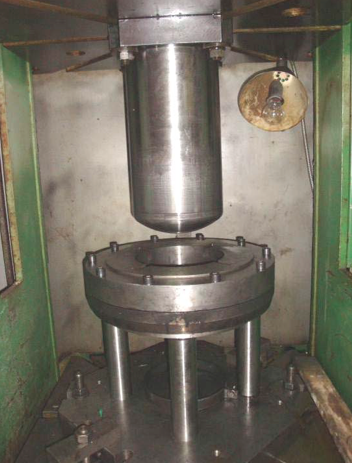
Attachment | Size |
---|---|
![]() | 308.83 KB |