Development of the methodic and model of the vibroacoustical signal processing system for the information-diagnosis complex of rotation systems
The two-level vibration control system of complex rotation systems (aviation engines) is developed at the steady-state and non-steady-state modes of operation. At the first level the vibration control system supports the current control of actual levels of vibration at the harmonics of the rotor rotation. The second level is assigned for analysis of “normal vibration” in order to predict or detect small damages of engine rotary details on the bases of integrated usage of signal processing methods for damages diagnosis. The vibration control method is based.
The synthesis, simulation and analysis of the digital narrowband tracking filter are carried out for the first level of vibration control system. The filter has a finite impulsive characteristic and supports the necessary pass bandwidth (from 2-3 Hz to 4-5 Hz) and necessary level of the off-frequency rejection (minus 30 dB).
The theoretical explanation of the usage of signal processing methods are carried out for the second level of vibration control system. There are following signal processing methods: Higher-Order Spectral and Statistical analysis; Time-Frequency Transformation; Scale-Time Transformation and determination of Dimensionless Peak Characteristics. These methods are using at the steady-state and non-steady-state modes of operation. We propose the integrated usage of signal processing methods on the basis of Wavelet Transformation and Statistical characteristics for the sensitivity enhancement of the Dimensionless Peak Characteristics at the initial damages propagation.
The software model of the two-level vibration control system is developed as the virtual device at the system of programming LabView. The model of vibration control system is developed. The technological and application software are developed. The lab test of developed model of the vibration control system is carried out.
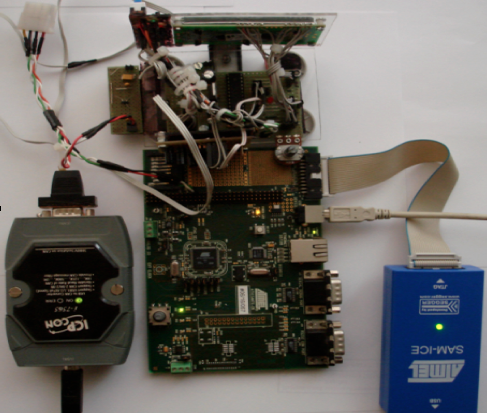
Долучення | Розмір |
---|---|
![]() | 434 КБ |