Technological bases of high-performance workpiece production and cold stamping of products with variable wall thickness
Mathematical models have been developed and structural and technological parameters of new high-performance technologies of waste-free separation of high-quality rolled products by blanks cut off in presses have been established. Designs of die tooling have been developed for cutting workpieces for subsequent stamping of products with variable wall thickness in height. Mathematical models have been created, the influence of structural, technological and physical-mechanical factors on the processes of cold and hot forming of hollow products with variable wall thickness by operations of back extrusion, drawing with thinning and compression has been investigated. Structural and technological parameters have been established which allow to reduce the deformation efforts, to increase the degree of deformation in one transition and to reduce the number of transitions of cold and hot stamping. On specific examples of cold forging of hollow products of small diameter from steels 10, 20, 11YA, hot forging of medium diameter of steel C-60 and cold and hot forging of hollow products of large diameter of L70 brass and high-strength aluminum alloy B93pch, new manufacturing technologies have been developed. Stamping equipment for the implementation of these technologies at the existing enterprises of Ukraine is calculated and designed. This ensures that the shape of the products is obtained and the necessary working of the structure of the metal along the height of the walls and in the bottom parts is achieved to achieve the mechanical properties of the deformed metal. New technologies for manufacturing small diameter 11YA steel and large diameter alloy B93pch have been tested by industry. The concept of manufacture of products with change of wall thickness is created, which allows to reduce the number of transitions of stamping and to significantly reduce the cost price of products.
A new highly efficient bimetal manufacturing process has been developed, based on the integrated use of laser radiation energy and the energy of the induced electromagnetic field. A new method for manufacturing bent bimetals using a powerful energy source for connecting plates has been created. A new method for manufacturing bent bimetals using a powerful energy source for connecting plates has been created. A number of original methods have been developed and implemented for the manufacture of bimetals by connecting individual sections of their components by welding using powerful energy sources, or by manufacturing special retaining elements and melt pouring the second component of bimetal. A number of technologies have been developed for the production of lightweight bimetals, which provide significant material savings, a significant reduction in the cost of their manufacture while ensuring the necessary adhesion strength of the components.
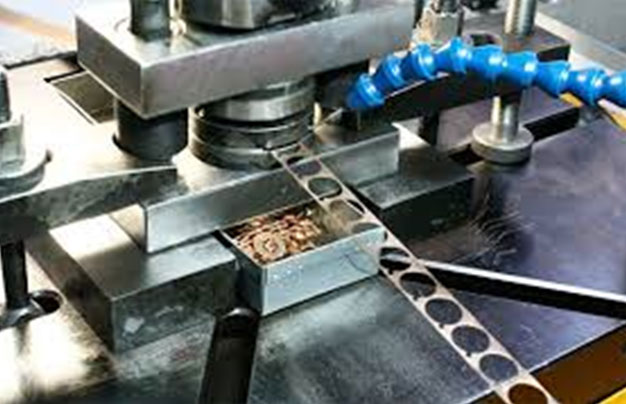
Attachment | Size |
---|---|
![]() | 273.81 KB |