Physicochemical bases of low-temperature synthesis (700 - 1500 оС) of ultra-refractory high-strength reinforced ceramics and metal-ceramics of multifunctional application
An integrated approach to the creation of scientific physicochemical foundations of the process of synthesis of large polycrystalline samples or products of reinforced ceramic high-temperature materials at low temperatures is implemented, which involves the use of a capillary-porous body with predetermined structural-geometric characteristics of pore channels as a medium for growing fibers reinforcement (the first at the level of separately taken powder particles from which a capillary-porous t is made) ceramic composite. The kinetic parameters of the growth process of refractory grains B4C, SiC, SiB6 in the silicon melt in the presence of a temperature gradient have been established. It is shown that increasing the velocity from 5 mm/min to 10 mm/min leads to an increase in boron carbide grains due to the nonequilibrium phase B12(SiBC)3, which is represented as a rim structure. It is shown that, depending on the velocity of the field of the temperature gradient, the microstructure of the obtained ceramics changes. Thus, at a minimum speed (0.5 mm/min), almost monolithic boron carbide is formed. With increasing speed up to 1.5 mm / min, there is a grinding of boron carbide grains compared to the minimum speed. The influence of crystallization rate on the process of microstructure formation of reinforced metal-ceramic Ti-TiB composite was investigated. It was found that increasing the crystallization rate leads to a change in the microstructure, namely, the higher the crystallization rate, the smaller the fiber size and the larger the number. With increasing crystallization rate from 0.5 mm/min to 4 mm/min the number of fibers in the alloy increases from 16% to 37%. New reinforced composites have been developed in the B4C(SiВ6)-SiC system, which is not inferior to hot-pressed hardness and has a flexural strength of about 500 MPa. The obtained materials can be successfully applied to products operating in conditions of dynamic, thermal loads and chemically aggressive environments, which are realized at the edges of the glider parts of unmanned aerial vehicles at the entrance to dense layers of the atmosphere, in rocket engines of special military and civilian equipment, in military and process engineering the interaction of the bullet with the material of the armor or barrel of small arms, in the cones of protection of the bow of the rockets, in land-processing, mining and metallurgical equipment.
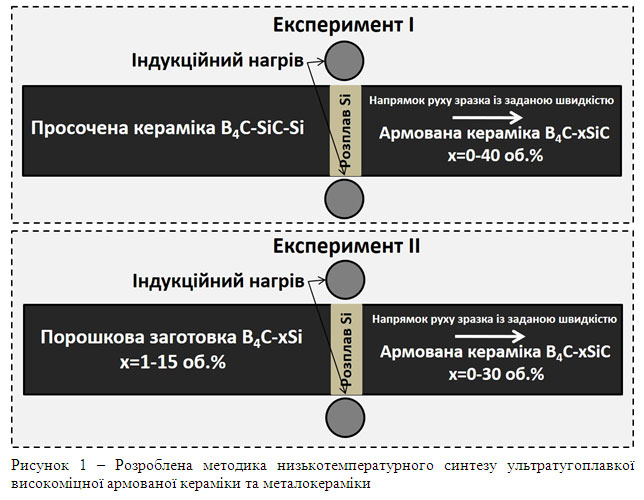