Increased productivity of manufacturing products in the processes of sheet metal forming
Reducing the number of transitions of manufacturing products and the increase in the degree of deformation at a transition in shaping sheet metal forming processes can improve the performance of manufacturing and makes the resulting products competitive.
For the drawing process developed ways of shaping with the use of differential radial flange backwater using liquid drawing in a die of special profile and the combined drawing in the double cone die special profile. Using computer simulation by the method of finite elements, was found that application of backwater significantly reduce the amount of tensile stresses in the dangerous section, which result is the destruction of the wall. Reduction of these strains has increased the degree of deformation in one transition and reduce the number of drawing transitions. The use of traditional drawing in a die of special profiles and combined drawing in double-cone die of special profile also reduced the number of presswork transitions. The experimental results confirmed the results of the calculations. Was found the analytical dependences for determining the parameters of the combined drawing in the double-cone die.
For processes of reducing tubular and hollow bottom blanks were used the application of liquid back pressure to the inner surface of the blanks and reducing was applied in the die of special profile. Calculation found that counter-pressure application with reducing of tubular of steel billets leads to the exclusion of loss of stability of the preform wall and forming of the cross-ribbed on the wall and on the deformed part of the workpiece, which allowed to obtain products with the neck in one transition. During reducing was applied cone and spherical dies of special profile. In such dies deforming surface is formed by the intersection of the circles of constant diameter whose centers are positioned at an angle with a certain step. Forming on these surfaces ensure the reduction of the friction forces in forming and increasing the degree of deformation in one transition. Using the pre-operation profiling wall of tubular or hollow blanks with the bottom results in reducing products of constant wall thickness. Prototypes of products was obtained by experimental way. Was founded the analytical dependences for determining the reducing force, the shape and size of the deformed part of the blanks.
The developed method of outward flanging of the holes in the sheet metal blanks and profiles provides receiving of deformed part with a constant wall thickness without distortion. Constant wall thickness leads to an increase in the height of products after outward flanging with thinning and increased reliability and durability detachable and permanent joints which are formed by outward flanging products with other items. Using the pre-profiling of the blanks and profiles by cold extrusion forming holes followed by punching jumper leads to saving metal. Calculations and experiments have shown the possibility of obtaining constant wall thickness. For engineering calculation of parameters of preliminary profiling blanks and parameters of outward flanging was founded analytical according to the definition of power modes, the specific efforts on the instrument and final shape and size of deformed blanks.
For various configurations of flanges on tubular workpieces and pipes was developed method of bulging by punch of special profile. At such punch deforming surface is formed by the intersection of the circles of constant diameter whose centers are located at an angle to the corresponding step. By computer simulation was found and confirmed by experiment punch profile, which provides a reduction of the friction forces in the forming in the bulging processes and increase the bulging ratio.
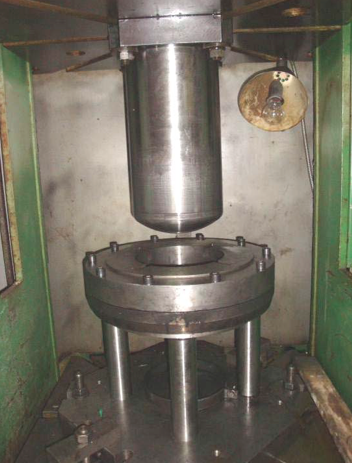
Attachment | Size |
---|---|
![]() | 308.83 KB |