Creation of breakthrough technologies for manufacturing components of irregular shape from composite materials for extreme operating conditions
The fundamentals of non-trivial additive technologies of 3D-printing and cold spraying (CS) for the manufacture of complex-shaped products from cermet and ceramic composites, as well as from multicomponent metal alloys, which are fundamentally different from existing analogs of costly foundry methods ensure the level of material properties required for their operation at temperatures above 600 °C, under conditions of high-speed multiple heating-cooling (1500 deg/min), cyclic loading and in an aggressive oxidizing environment.
The developed technologies are based on the implementation of a step-by-step production cycle: 1) production of powders from composite cermet materials and high entropy alloys (HEA) with a composite structure for further use in 3D-printing or CS methods; 2) fabrication of a frame workpiece with a predetermined geometry, porosity and pore morphology via layer-by-layer 3D-printing of the obtained powders or the formation of a composite material by the CS method; 3) manufacturing of parts by impregnating porous frame blanks or prototype models with matrix melt to obtain a composite of a multilevel hierarchical structure. The fabrication of a framework using layer-by-layer 3D-printing of powders opens up the possibility of varying the content of the reinforcing phase within wide limits and manufacturing ultra lightweight products of complex shape from high-temperature materials at relatively low temperatures, which is currently unattainable for any known method.
The optimal technological parameters of the fabrication process of frame materials (chemical and phase composition, structure of initial materials, power and duration of exposure to the laser beam, powder layer thickness, method of its feeding, temperature and heating time, printing speed, temperature-time parameters and method of impregnation, dimensional characteristics of the reinforcing frame), providing high performance. For the first time in world practice, the possibility of consolidating a high-hardness (7.6-10 GPa) HEA powder with full preservation of the nanostructural state and phase composition has been experimentally substantiated as a result of the application of innovative CS technology.
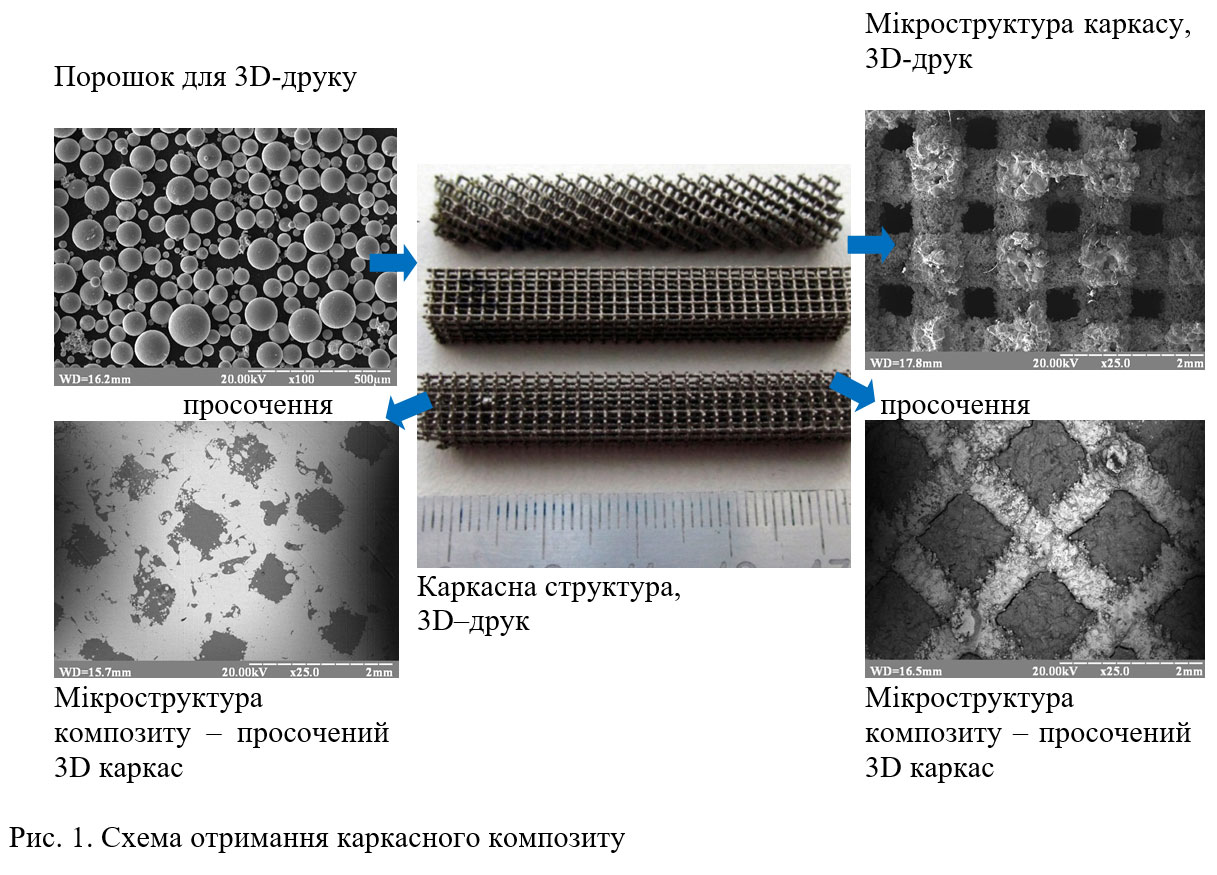
Attachment | Size |
---|---|
![]() | 595.41 KB |