Development of disk connections between billets in columns and energy-efficient graphitizing regulations for electrodes in direct-heating furnaces
The requirements for electric contact joints between workpieces in the core columns of Kastner furnaces are formulated. The choice of a material - graphite foam - for making electric contact gaskets is justified. Rational form and thickness of electric contact pads have been determined, the glue for their fixation between electrode blanks has been selected. A mold for forming electrocontact pads has been developed and prototypes of pads of different shapes, thickness and density have been made in order to check their suitability for forming Kastner furnace core under industrial conditions. Experimental dependences of specific electrical resistance (resistivity) of electric contact pads and contact resistance of "blank-pad" pair depending on pressure and temperature were obtained. Rational thickness and density of electric contact pads have been determined experimentally. Innovative high-tech core-core formation measures outside Kastner furnaces consisting of electrode billets and electrocontact joints between them have been developed. Mathematical and numerical models of the thermoelectric state of direct heating furnaces during graphitization of electrode billets are refined, which take into account the dependence of the resistivity of the connections and the contact thermoelectric resistance between the billets and spacers on the pressure and temperature. Using the developed Kastner furnace model for the numerical analysis of the physical fields of the graphitization process, the intensified regulations of graphitization of electrode billets in the columns connected by new electrocontact spacers are developed. Experimental testing of the developed technical solutions on the operating industrial equipment is carried out. The effectiveness of the proposed technical solutions to modernize the method of core formation and intensify the regulations of the electrical power supply of Castner furnaces is determined, which includes the reduction of specific electricity consumption and the output of defective products.
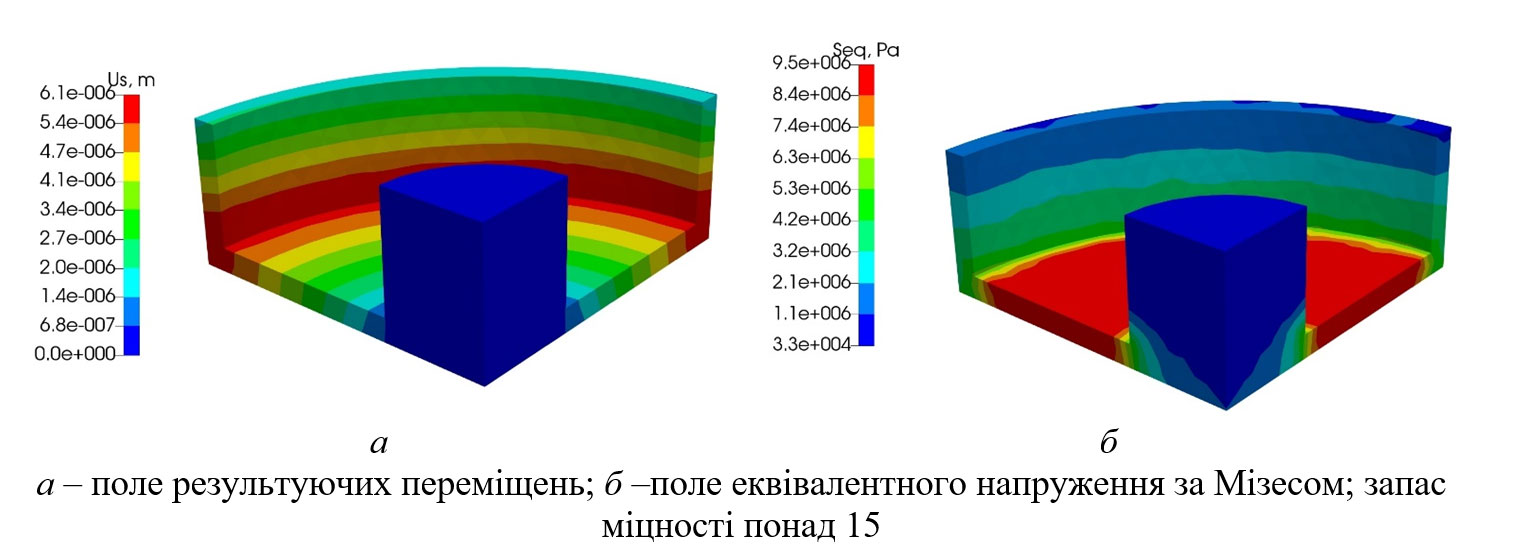
Attachment | Size |
---|---|
![]() | 322.26 KB |