Creation of thermophysical bases of design of heat exchange devices on two-phase heat transfer elements for energy saving in ventilation systems of buildings
Experimental samples of flat-oval thermosyphons (TS) with partial transverse rectangular and corrugated finning and samples of round TS with inner intensifiers of heat transfer in evaporation section (ES) were developed and fabricated. They are intended for functioning in heat exchangers (HE) utilizers of heat wastes in ventilation systems. It was shown, that freon R134a is the most optimal heat carrier for TS functioning in conditions close to these in ventilation systems from the point of boiling temperature and safety of application. The most optimal parameters of outer finning from the point of combination of high heat-aerodynamic characteristics and minimal weight of heat transfer surface are: fin length – 50 mm, fin height – 20 mm, fin thickness – 0,3 mm, fin pitch – 3 mm. Experimental investigations have shown that designed TS are able to transfer up to 200…220 W of heat energy and their thermal resistance is in a range 0,05…0,07 K/W. Thermal resistance of proposed TS is on 35…92% lower and transferred heat power is on 29…46% higher than these of analogues described in literature. These TS can be applied at air velocity from 1,8 m/s to 20 m/s at temperature difference between supply and exhaust air 10…28°C and also at negative temperatures of supply air. Obtained characteristics of TS make them attractive for application as a main heat transfer elements of HE-utilizers. It was experimentally shown, that 3 times increasing of length of ES with simultaneously 3 times decreasing of filling ratio (FR) leads to 1,3…2 times decreasing of TS thermal resistance. That’s why it was recommended to apply in HE-utilizers TS with ES length 150 mm (ratio between length of ES and condensation section 1:1) and FR equal to 58%. Also it was found out that application of inner intensifiers of heat transfer in ES in form of thread leads to 2 times increasing of transferred heat power when compare it to smooth surface. This makes it possible increasing of HE-utilizers heat power without increasing of TS quantity. Empirical correlations for heat transfer intensity in ES of flat-oval TS with freon R134a as the heat carrier were obtained. Also, known method of TS thermal resistance evaluation was modified in order to adapt it for calculation of thermal resistance of proposed TS intended for application in HE-utilizers of heat wastes in ventilation systems. Experimental mock-up of HE-utilizer was developed and fabricated. It has: high efficiency in wide range of temperature difference between supply and exhaust air 10…28°C and at negative temperatures of supply air; high grade of outer surface development and high compactness; 2…2,5 times lower aerodynamic drag than that of round finned tubes; close to ideal contact between finning and base tube; high corrosion resistance; simple manufacturing technology and can be applied at wide range of heat power. Empirical correlations in dimensionless form for calculation of outer heat transfer intensity and aerodynamic drag of the mock-up were proposed based on the results of experimental investigations. Recommendations on designing of HE-utilizers based on flat-oval TS with partial transverse finning were developed and proposed based on the results of the study.
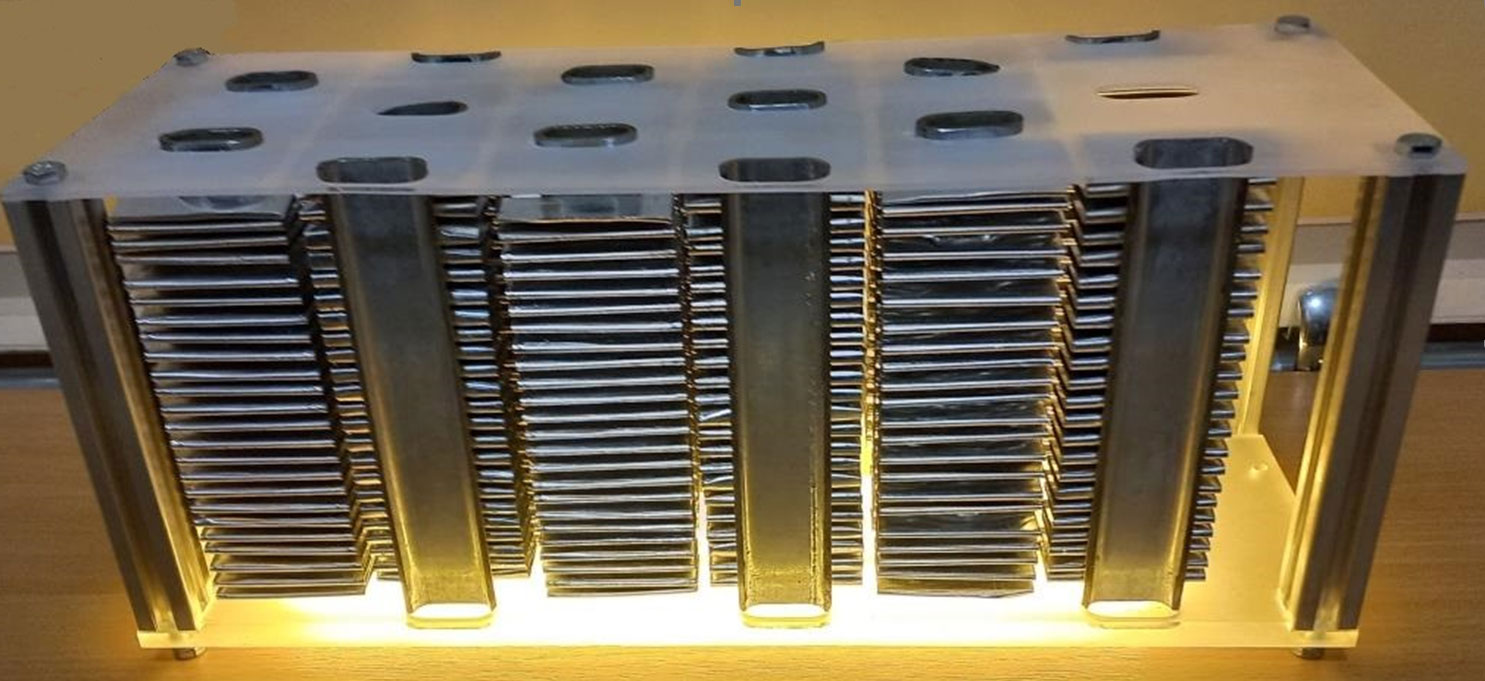
Attachment | Size |
---|---|
![]() | 290.82 KB |