Development equalincreased heat transfer surfaces for gas turbine regenerators of gas transport systems and research their heat-aerodynamics characteristics
Gas turbine unit ( GTU) is the dominant type of drive gas transportation system of Ukraine. However, most of them morally and physically obsolete, leading to a waste of gas for its own needs, which in 2010 amounted to 4.9 billion m3. To improve gas turbine is to use the least expensive stoves (regenerator) for utilization of heat in the turbine exhaust gases at the same time regenerators at current levels of use are bulky often have low operational reliability. The creation of new turbine with high technical and economic parameters or modernizing impossible without the use of their designs reliable and efficient heat transfer surfaces. Such requirements are met by developed new surface - helical tube equal the developed surface.
Within the offered research designed and manufactured laboratory models of helical-shaped tubes knurled by three rollers with the developed surface surface with different geometrical characteristics by using relatively cheap technology.
Studies of hardness and its tube wall thickness after deformation. The experimental results showed that the greatest intensity of stress and strain achieved by the rounded edges of the roller tube screw fracture appears in the greatest depth of the groove (h ≥ 5 мм) at maximum deformation εк ≥ 0,6.
The structure in the form of flow lines flow on the surface of tubes. The results of flow visualization revealed the existence of three-dimensional vouchers zones and vortex structures that are effective in generating additional turbulence in the boundary layer and the flow as a whole.
Experimental study of convective heat transfer and aerodynamic resistance of the investigated package helical tubes suggest that the intensity of the heat tube depends on the geometry and characteristics of stepper package. Depending on the operating conditions is 10-30 % higher than for similar in layout smooth round tubes.
According to experimental results obtained by calculation methodology and aerodynamic resistance to heat transfer surfaces helical tubes. A methodology based on generalized empirical dependences for calculation of heat transfer coefficients and pressure losses external and internal coolant for heat exchangers such as "gas-gas". Proposed guidelines on technology of spiral tubes knurled by three rollers thin smooth round tubes.
Results teploaerodynamichnyh calculations showed that the surface of the helical tube can increase the compactness of the heat exchanger by (30-40) %, which reduce the overall size and weight.
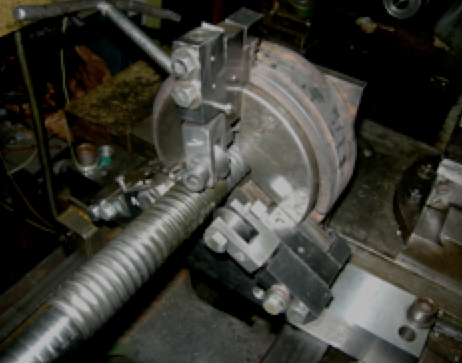
Attachment | Size |
---|---|
![]() | 236.5 KB |