Innovative technologies and machine tool equipment for highly productive cutting by cutting modern structural materials
When implementing the project, a comprehensive research structure was applied, in which the choice of a specific type of research was determined by the goals and objectives that were solved at individual stages of its implementation. First, when developing mathematical models of the processes of shaping by cutting, an approach based on numerical and simulation modeling was used, and experimental design methods and regression analysis were used to determine some empirical parameters of the models. Secondly, in developing dynamic models of spindle units, a systematic approach was used, which considers the spindle unit as a complex system taking into account the cutting process and the surrounding elements of the entire technological processing system. Thirdly, in the search for innovative solutions for machining composite materials, the experimental research method was used to verify effectiveness and establish adequacy.
The theoretical foundations of controlling the cutting process have been created, aimed at solving the optimization problem, which are divided by the time the information used to form the control is received. In the course of research, it turned out that the most effective method of achieving the required accuracy of machining parts of a complex contour in the conditions of uncertainty of the parameters of the technological machining system is control by a posteriori information.
The basics of control by a posteriori information have been developed, involving the use of the capabilities of modern CNC machines, software has been created to automate the design of adjusted machining paths, virtual-based, which have been practically tested on machines of a turning and milling group, in particular ST-20 MF-3 HAAS.
A generalized dynamic model of the machine tool spindle assemblies as a complex mechanical oscillating system containing the subsystems of the tool, the workpiece, the spindle on the supports and the body mounted on the bed is developed. This constitutes the theoretical basis for the creation of new, more advanced methods for assessing the dynamic state of spindle units.
Created innovative technologies for machining composite materials provide for the use of new tooling, which was developed for drilling operations with process optimization and the expansion of functional and technological capabilities
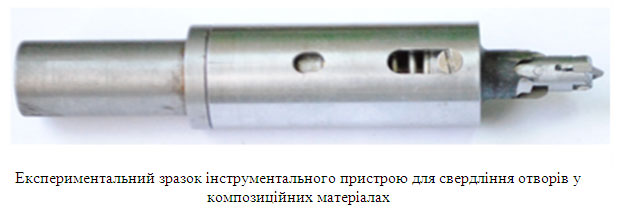
Attachment | Size |
---|---|
![]() | 435.2 KB |