Creation of resource-saving processes and installations for isothermal viscoplastic molding of titanium alloys and powder materials of parts with thin-walled elements in mechanical engineering
Creation of resource-saving technologies and equipment for forming parts with thin-walled elements from titanium alloys and powder materials, for example, monolithic wheels and blades of gas turbine engines and others, with high accuracy and specified operational properties. Such a problem regarding serial technology for titanium alloys is being solved for the first time in the world.
On the basis of the accepted working hypotheses of the work, modern research problems, the latest solutions were formed regarding effective schemes, resource-saving processes were developed on the basis of new knowledge about the viscoplastic flow of titanium alloys and powder materials in isothermal conditions, recommendations were developed regarding the selection of the temperature-velocity factor, deformation modes and created methods for the implementation of the technological process of manufacturing parts with thin-walled elements for industrial enterprises in the aviation industry.
Today, the main processes of manufacturing unicycles are mechanical processing from a monolithic workpiece, which is highly labor-intensive for aluminum unicycles up to 200-250 hours, and for titanium 250-350 hours on CNC machines. The use of new knowledge reduces the labor intensity of production by 40-80%.
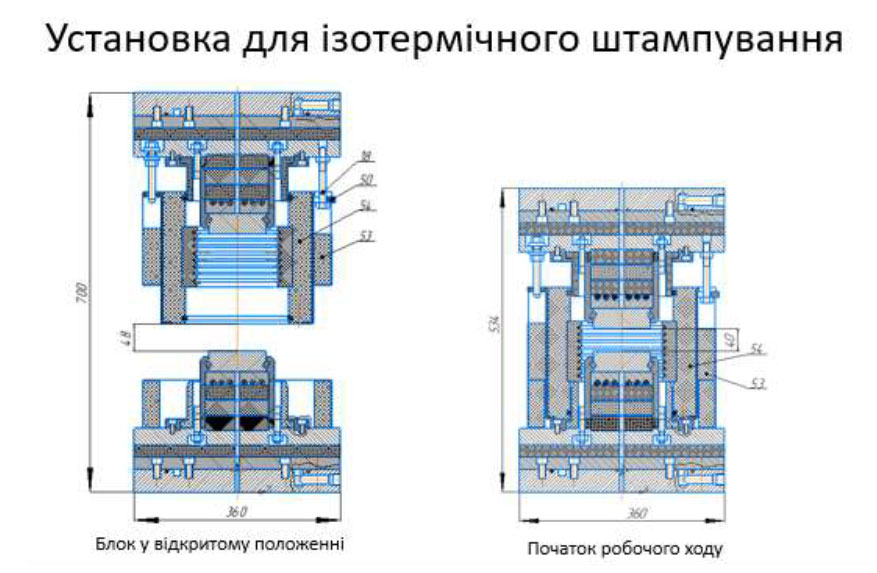
Attachment | Size |
---|---|
![]() | 383.08 KB |