Моделирование процессов межфазного взаимодействия при электродуговой сварке и наплавке под флюсом
Показано, что для оценки металлургических свойств флюсов при электродуговой сварке в большинстве моделей ограничиваются рассмотрением реакции шлак-металл, что противоречит физической модели электродуговой сварки под флюсом. Существование газовой фазы и ее влияние на химические процессы на межфазных поверхностях игнорируется.
Установлены особенности формирования газовой фазы как определяющей составляющей металлургических процессов при электродуговой сварке под флюсом. Проведены термодинамические расчеты реакций на межфазных границах газ-металл, газ-шлак, шлак-металл, на основе которых определены приоритетные реакции и проведена температурная и межфазная структуризация реакционной зоны сварки согласно предложенной физической модели. Впервые создана термодинамическая модель, которая состоит из четырех взаимосвязанных групп реакций, на основе которых формируется единая система нелинейных уравнений, которая в результате определения констант равновесия каждой реакции и заданном содержании компонентов в сварочных материалах позволяет рассчитывать химический состав металла шва и прогнозировать свойства межфазной границы шлак - метал для управления сварочно-технологическими и металлургическими свойствами шлака. Разработаны алгоритмы и схема расчета металлургических процессов, происходящих в газовой фазе и межфазных границах газ-металл и газ-шлак. Показано, что с помощью разработанного алгоритма расчета металлургических процессов в реакционной зоне сварки возможно определять химический состав металла шва в «нулевой точке». Для учета влияния режима сварки на особенности формирования состава металла шва необходимо использовать принципы неравновесной термодинамики, которые в данном случае с математической точки зрения могут быть описаны полиномиальными уравнениями второго и третьего порядка, коэффициенты которых определяются на основе литературных или экспериментальных данных.
Проведен анализ шлакового расплава с точки зрения ионного строения шлаков, возможностей образования квазинейтральных молекул и наномицел. Это позволило определить особенности поведения определенных окислов флюса в шлаке и их соотношение. Выбрана комплексная оксидная система для создания флюсов. На этой базе определена граница содержания отдельных компонентов для оксидной шлаковой системы SiO2-TiO2-MgO-CaO-Al2O3-MnO-Fe2O3-ZrO2-CaF2. Выбран состав и модуль жидкого стекла
Для изготовления опытной партии агломерированных флюсов выполнены расчеты параметров режима работы гранулятора и доокатывателя. Проведены исследования по влиянию режима предварительного доокатывания на прочность зерна флюсов на основе которых оптимизирована технология их изготовления. Изучен вопрос сорбирование влаги от времени доокатывания флюсов и его удаления из зерен флюса. Установлено оптимальное время прокаливания. С помощью компьютерной обработки данных оптического микроскопического анализа зерен флюсов с различным содержанием компонентов определены особенности обволакивания частиц шихты жидким стеклом и установлена зависимость коэффициента обволакивания от содержания оксида циркония. Изучены сварочно-технологические свойства экспериментальных модельных флюсов. Экспериментально определена активность кислорода в шлаковом расплаве, металле шва, содержание кислорода в металле шва и легирующих элементов. Проведенны исследования по изучению таких физических свойств шлаков экспериментальных флюсов как вязкость и угол смачивания. Приведены объяснения полученных результатов с точки зрения ионного строения шлаков.
В результате выполненной работы созданы принципы разработки новых сварочных флюсов с регулируемой окислительной способностью и улучшенными сварочно-технологическими свойствами, разработана методика определения химического состава металла шва, которая базируется на термодинамических уравнениях химических реакций на межфазных границах.
На основе проведенных исследований создан агломерированный флюс для наплавки деталей сложной конфигурации с улучшенной отделимостью шлаковой корки при повышенных температурах. Разработаны и зарегистрированы технологические условия ТУ У 24.6-05416923-101:2011 на изготовление и применение флюса АНК-73. Флюс прошел опытно-промышленное испытание.
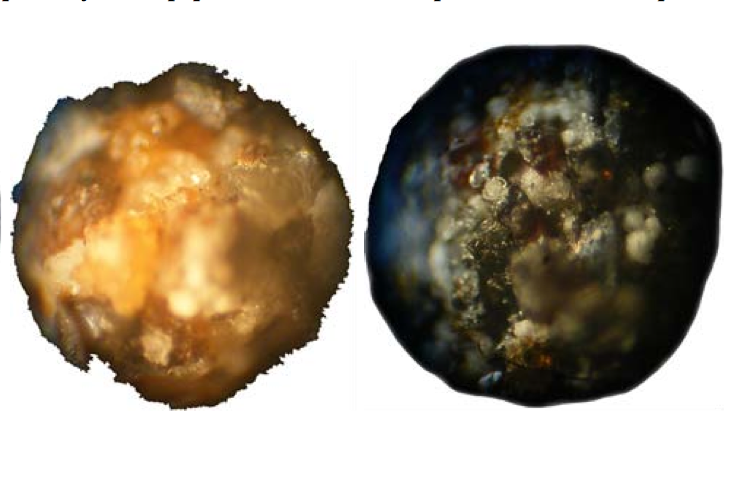