Development of the generalized lifetime prediction method for composite structural elements at complex low-cycle loading with damage
The main result of work consists in development new physical equations theory of cyclic elastic-viscos-plasticity at complex technological and operational thermo-power loading; methods of theoretic-experimental lifetime calculation new products and residual lifetime definition of the responsible high-loaded designs elements machine-building complex different function at a stage of their operation.
The new generalizing model of scattered damages accumulation kinetics in CM for complex stress state conditions, method, algorithm and the software on lifetime prediction of o objects and designs operation from CM at a stage of their design and a residual lifetime at a stage of their operation is theoretically proved.
As research work result, it received:
- For the first time the new phenomenological model of damage accumulation kinetics in CM for complex low cyclic loading (deformation) conditions which is based on solid mechanics, thermodynamics of irreversible processes, continuum damage mechanics, the theory of probability and mathematical statistics is developed and proved.
- For the first time the power type, rupture criterion for anisotropic CM (at a stage of macrocrack initiation) developed for complex low-cyclic loading conditions.
- For the first time it is established that in the conditions of repeated-variable loading (deformation) in CM pass processes of accumulation and “closure” of microdamages. The corresponding quantitative and qualitative damage parameters, which considered in the kinetic equation and rupture criterion, are established.
- For the first time the matrix of additional change of volume and form of the CM RVE, which caused by scattered damage, accumulation for repeated-variable complex loading conditions received and proved. Matrix of change volume and form transformation carried out at a reverse damage process to a matrix of damage function.
- Proved, for the first time, communication of damage function matrix with deformation and stress tensor. Established that the damage function matrix correlates with damage function tensor for reverse loading (deformation).
- For the first time received invariant values, which characterize damage parameters in a general view of a complex stress state. They based on two rupture mechanisms: tear and shear.
- For the first time received ratios for definition of “closure” factors in CM for repeated-variable loading conditions. Established that for stress controlled low-cyclic loading the mentioned factors are higher in comparison with it for strain controlled. Established their quantitative characteristics for a number of CM depending on their main physic-mechanical characteristics.
- Carried out modernization of test machines and improved the continuous diagnostics of scattered rupture kinetics technique for different trajectories of program low cyclic loading (deformation) taking into account anisotropy of the CM main physic-mechanical properties.
- Developed the method, algorithm and software (based on FEM) on lifetime prediction of designs elements from CM on parameter of low-cyclic fatigue at a stage of their design and a residual lifetime at a stage of their operation.
- Solved important tasks in the applied plan on lifetime prediction of the high-loaded designs elements of aircraft glider and a precision separator in cyclic statement (based on 2105 cycles). Comparison of settlement results of program low-cyclic fatigue with natural experiments showed their satisfactory coincidence.
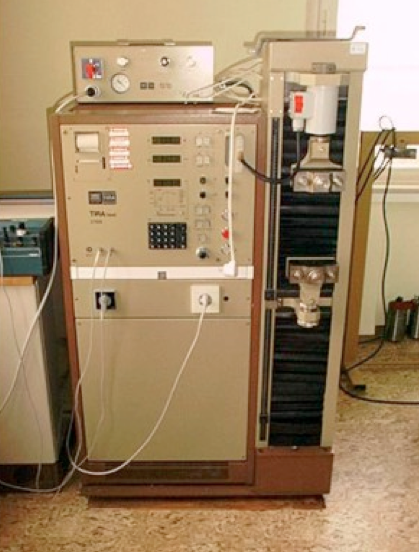
Долучення | Розмір |
---|---|
![]() | 1.46 МБ |