Development of the eco-efficient and resource-saving technology for obtaining and finishing of wear-resistant parts based on waste silumins for printing machines
Developed environmentally efficient and resource-saving technology for producing and finishing fundamentally new wear-resistant composite parts for use in nodes of post-printing equipment based on the grinding of waste aluminum alloys - silumins with solid lubricant (or without) allows to manufacture new parts that wear resistance significantly exceed the known parts which operatt in similar conditions. Developed technology is based on the use of powder metallurgy processing steps in combination with precision machining of the friction parts’ working surfaces. According to the research technological operations of regeneration of secondary raw materials from aluminum sludge waste, technological modes of cold and hot pressing pieces of new parts have been developed, that allows to control the structure and properties of new materials. Determiniation the influence of synthesis technology of composite parts on the mechanism of antifriction friction film’s self-lubricating during operation allows to realize the directed tribo synthesis that is the determining factor for the stability of high-wear parts in the working conditions in friction without oil lubrication.
Calculated mathematical relationships allowed to obtain the computer models of the technological modes for finish machining of the new parts’ working surfaces of recycled waste silumins that take into account the processes of thermal contact interaction of the grinding wheel’s cutting abrasive grains and the formation of heat sources, affecting of the surfaces’ quality parameters of new composite parts based on grinding waste at the supercomplex grains’ trajectory in the working area of treatment.
Waste processing methods allow to create and control the formation of working contact surfaces’ microrelief of new composite parts for ensuring the high quality parameters of the surfaces, which is a prerequisite of high wear resistance for new friction parts at the operating conditions of post-printing machines.
According to the research the typical technological processes have been developed and produced a pilot batch of samples - guides and brackets based on recycled and reclaimed materials for the implementation on the enterprises of machine-building industry.
As a result of the new parts’ introduction a marriage of the printed products decreased from 2.0 to 1.02%. The total economic effect of the introduction of research results amounted to about 175 thousand UAH in a year.
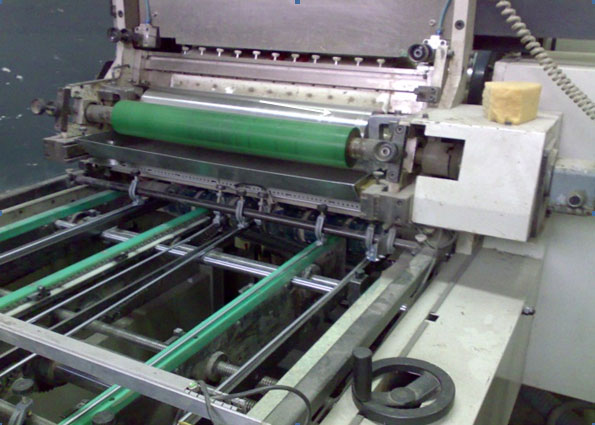
Attachment | Size |
---|---|
![]() | 532.22 KB |